The third group of students is about to finish its course in the aircraft manufacturing laboratory. Here, the students experience the norms and standards of the aviation industry.
Danielle de Jong pulls a rivet. (Photo: Sam Rentmeester)
The hangar of the Aerospace Engineering Faculty feels like a museum of aviation. A F16 fighter, wings, cockpits, and engines are spread throughout the large hall. But climb the stairs, and open the electronic lock with a card and you’ll enter a different world entirely. The aircraft manufacturing laboratory feels like an operation theatre with people dressed in white lab coats, spotlessly clean floors, and blue plastic covering aluminium panels. On the middle table lies not a patient, but the tailpiece of an aircraft under construction. Weird copper-coloured sticks protrude perpendicularly out of the fuselage. Half a dozen of students are at work, deeply concentrating and working slowly. The assembly of an airplane is a step-by-step process that is verified and documented in every single step of the way.
Danielle de Jong, one of the students, explains that the blue plastic protects the thin aluminium panels from scratches. Besides the plastic, every part of the panels that comes into contact with another piece is protected with primer. “A scratch can develop into a crack,” she explains, “or it exposes the material to erosion.” So scratches are not allowed. Aluminium panels are fixed to the ribs and to each other with rivets. But there are a dozen ways you can fit rivets askew, crooked, lop-sided or awry. None of these is allowed. That’s why every single rivet is inspected and corrected if need be.
Students from the smartphone generation are less dexterous than earlier generations
Professor Sybrand van der Zwaag, one of the four project mentors, explains: “When one student pulls a rivet, two others will look if he positions the rivet at a right-angle to the surface.” Teamwork is important. “Students working here must have the courage to correct each other and to report failures. There’s only one thing worse than making failures and that is not reporting them.” If something goes wrong, students need to solve the problem in such a way that the correction is traceable to inspections. Every step of the assembly is inspected and filed. The files and the workpiece get periodical reviews from two official external inspectors.
It’s all part of the norms and values of the aircraft manufacturing industry. Danielle de Jong says: “I knew in principle that the industry works like that, but I had not seen it in practice. Reporting and verification sometimes take longer than the actual work.”
Van der Zwaag observes that students from the smartphone generation are less dexterous than earlier generations. “They have to learn real basic skills before they can work on the assembly.” That’s why every student starts by making his own toolbox. From riveted aluminium panels of course.
For students, the aircraft manufacturing laboratory is mostly a practical twenty week Friday project. Up to now, the course was open to AE students only. Van der Zwaag will consider applications from other faculties, such as 3mE, as well (see below). Required skills include precision, teamwork, responsible work attitude, and transparency.
As for the workpiece on the table, it’s the tail cone for a two-seater propeller airplane, the VAN’s RV 12. It will have a span of eight metres by six metres long. The empty weight is 350 kilograms, the maximum weight 600 kilograms. It will be powered by a 100 hp engine.
The mentors from the AE structures and materials department, and the flight performance and propulsion department (Sybrand van der Zwaag, Joris Melkert, Jos Sinke and Vincent Brügeman) estimate that ten student teams will work on the assembly over a four year period. After assembly, the aircraft will be sold to cover the expenses of the assembly kit.
- Students interested to join the next course (code: AE4ASM517) please contact Shanta Visser at S.P.Visser@tudelft.nl
VAN’s RV 12 Flight:
VAN’s RV 12 Test:
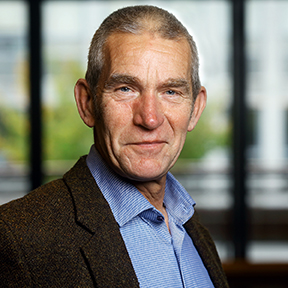
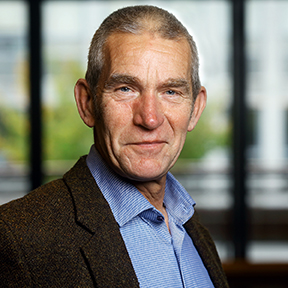
Do you have a question or comment about this article?
j.w.wassink@tudelft.nl
Comments are closed.