This week, students from TUD’s Faculty of Industrial Design Engineering (IO) meet mechanical engineering students from Slovenia and micro-engineering students from Switzerland.
Together, they’ll finish designing and manufacturing protective equipment for the global welding industry.
To design and manufacture a global product that can be marketed in various parts of the world; that’s the goal of the course ‘Global Product Realization’. In virtual classrooms, students from the Ecole Polytechnique Federale de Lausanne in Switzerland, the University of Ljubljana in Slovenia, and TU Delft, designed concepts for protective welding equipment. Over the past four months, the students video-conferenced with each other as they designed the initial concepts for welding helmets and air-suction units. This week, the students finally met in Delft.
One group of Dutch, Swiss and Slovenian students designed a ‘total concept’ for head, air and eye protection for the welder. In the facemask, fresh air is provided by a motorized filter that is either worn on the hip or attached to the helmet. A small fan in the front part of the helmet helps extract the exhaled air. For safe vision during welding, the students placed two small cameras at both sides of the helmet. Two LCD-screens positioned just in front of the welder’s eyes display the cameras’ images.
Welding company De Vlamboog gave the students the design assignment, stipulating that the finished products should be innovative and comfortable for the welder to wear. ”The main problem in the welding business is that legislation is getting stricter and the market is decreasing every year in Western countries. Because of the high wages and high work-safety health standards here, most welding is done in Asian countries,” says Ellis van den Hende, an IO student. ”In countries like Holland the trend in welding is towards reparation. When ships or trucks are broken, people weld.”
Global in a product, adds Van den Hende, means that the basic product can be used everywhere. ”People in Switzerland that don’t want to use the cameras should be able to change the cameras in the helmet for auto-darkening protective lenses,” she says. Auto-darkening lenses are made from a type of glass that turns black as soon as the welding starts. ”Or, someone can choose to wear the fresh-air unit at the back of his helmet instead of on his hip.”
In the huge entrance hall of the IO building, another group is working on a ‘butterfly’. According to Ivana Buble it’ll be a part of a mobile fume extractor. ”Most people weld in fixed places that are very well ventilated. With this model, people must be able to weld everywhere, in difficult places without needing a respiratory unit,” says the Slovenian mechanical engineer.
Their design consists of a large machine that is connected, via a pipe, to a small fume extraction mechanism. This small mechanism is not much larger than a shoebox and can be fixed to any wall by its magnetic part. Buble is working on the handgrips, which are made of polystyrene foam and will give the welders an ergonomic grip
Working closely together for one week, the differences between the students quickly become apparent. According to Buble, Delft students think more about the shape of the product, the color and if it’s economically feasible. ”We’re more practical and think a lot about how it will work,” she says. Van den Hende agrees: ”A Delft student almost immediately thinks ‘nice idea,lets work it out; we see the problems but we’re sure we can fix them somehow’. While the Slovenian students think in terms of solutions and will work out the idea more stepwise than we are used to.” The differences also have to do with the students’ varying academic backgrounds (mechanical engineering, micro-electronics or IO), all of which are needed to design every aspect of the various products
Upstairs, in Design room 7 of the IO building, Guylann Collet is busy working on an adjustable display unit for the welder’s eyes. Located inside the helmet, this mechanism allows the user to adjust the displays to suit his eyes. ”Everybody made different parts of the helmet at their university,” the micro-engineer from Switzerland says. ”Now, we’re all together, and we must make sure everything fits. And it must fit, no matter what it takes. Because this Friday we have to present our work at a symposium and exhibition.”
www.e-gpr.nl
23 May: symposium and exhibition, Landbergstraat 15, Delft. The exhibition runs until June 5th
This week, students from TUD’s Faculty of Industrial Design Engineering (IO) meet mechanical engineering students from Slovenia and micro-engineering students from Switzerland. Together, they’ll finish designing and manufacturing protective equipment for the global welding industry.
To design and manufacture a global product that can be marketed in various parts of the world; that’s the goal of the course ‘Global Product Realization’. In virtual classrooms, students from the Ecole Polytechnique Federale de Lausanne in Switzerland, the University of Ljubljana in Slovenia, and TU Delft, designed concepts for protective welding equipment. Over the past four months, the students video-conferenced with each other as they designed the initial concepts for welding helmets and air-suction units. This week, the students finally met in Delft.
One group of Dutch, Swiss and Slovenian students designed a ‘total concept’ for head, air and eye protection for the welder. In the facemask, fresh air is provided by a motorized filter that is either worn on the hip or attached to the helmet. A small fan in the front part of the helmet helps extract the exhaled air. For safe vision during welding, the students placed two small cameras at both sides of the helmet. Two LCD-screens positioned just in front of the welder’s eyes display the cameras’ images.
Welding company De Vlamboog gave the students the design assignment, stipulating that the finished products should be innovative and comfortable for the welder to wear. ”The main problem in the welding business is that legislation is getting stricter and the market is decreasing every year in Western countries. Because of the high wages and high work-safety health standards here, most welding is done in Asian countries,” says Ellis van den Hende, an IO student. ”In countries like Holland the trend in welding is towards reparation. When ships or trucks are broken, people weld.”
Global in a product, adds Van den Hende, means that the basic product can be used everywhere. ”People in Switzerland that don’t want to use the cameras should be able to change the cameras in the helmet for auto-darkening protective lenses,” she says. Auto-darkening lenses are made from a type of glass that turns black as soon as the welding starts. ”Or, someone can choose to wear the fresh-air unit at the back of his helmet instead of on his hip.”
In the huge entrance hall of the IO building, another group is working on a ‘butterfly’. According to Ivana Buble it’ll be a part of a mobile fume extractor. ”Most people weld in fixed places that are very well ventilated. With this model, people must be able to weld everywhere, in difficult places without needing a respiratory unit,” says the Slovenian mechanical engineer.
Their design consists of a large machine that is connected, via a pipe, to a small fume extraction mechanism. This small mechanism is not much larger than a shoebox and can be fixed to any wall by its magnetic part. Buble is working on the handgrips, which are made of polystyrene foam and will give the welders an ergonomic grip
Working closely together for one week, the differences between the students quickly become apparent. According to Buble, Delft students think more about the shape of the product, the color and if it’s economically feasible. ”We’re more practical and think a lot about how it will work,” she says. Van den Hende agrees: ”A Delft student almost immediately thinks ‘nice idea,lets work it out; we see the problems but we’re sure we can fix them somehow’. While the Slovenian students think in terms of solutions and will work out the idea more stepwise than we are used to.” The differences also have to do with the students’ varying academic backgrounds (mechanical engineering, micro-electronics or IO), all of which are needed to design every aspect of the various products
Upstairs, in Design room 7 of the IO building, Guylann Collet is busy working on an adjustable display unit for the welder’s eyes. Located inside the helmet, this mechanism allows the user to adjust the displays to suit his eyes. ”Everybody made different parts of the helmet at their university,” the micro-engineer from Switzerland says. ”Now, we’re all together, and we must make sure everything fits. And it must fit, no matter what it takes. Because this Friday we have to present our work at a symposium and exhibition.”
www.e-gpr.nl
23 May: symposium and exhibition, Landbergstraat 15, Delft. The exhibition runs until June 5th
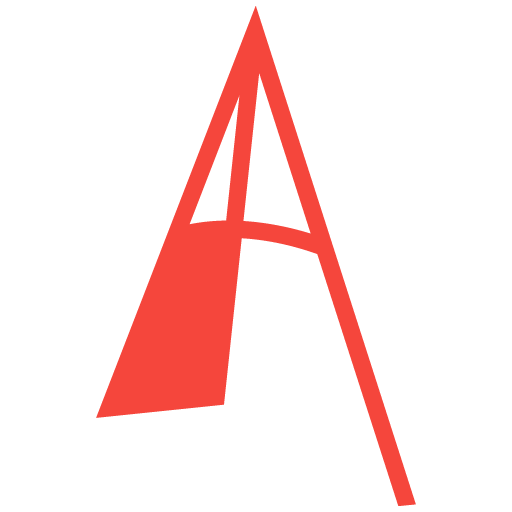
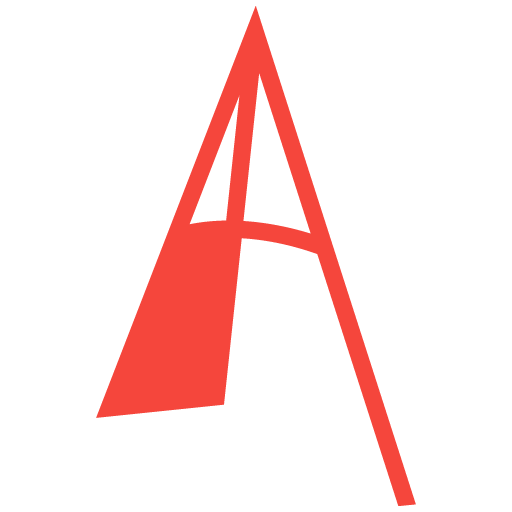
Comments are closed.