Can 3D-printing bring back a manufacturing industry to the US and Europe? People at the KiviNiria seminar “3D-printing: facts or fiction?” thought so. But what kind of manufacturing is that?
According to influential analysts, 3D-printing is at the top of its hype and the subject of a record number of media articles promising a third, fifth or sixth industrial revolution depending on one’s views. But after the hype, the products that emerge may prove disappointing. So, the KiviNiria’s seminar, organised by the industrial design chapter from the Dutch Engineers’ Association, and intended to separate hype for hope, was well timed. It was held in Amsterdam on 30 May 2013.
One successful enterprise in 3D-printing is the firm Shapeways, originating from Eindhoven Netherlands, which has seen 30 million dollars of capital investment. Shapeways recently started a shop in New York, which was opened by Mayor Bloomberg himself, who saw this as a welcome return of industry into the city. Via the website, customers can order 3D-printed objects made from plastic, steel, ceramics or silver. A large number of objects on the website may be tweaked to one’s own taste. In fact, that’s the technology’s star feature. It enables mass-customisation. You can 3D-print jewellery for your wife and toys for your kids.
What emerges from this are small customised items and a number of creative individuals making a home-industry and indeed sometimes a living from selling their designs. But can 3D-printing offer more than just a fun factory?
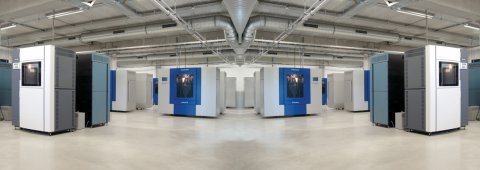
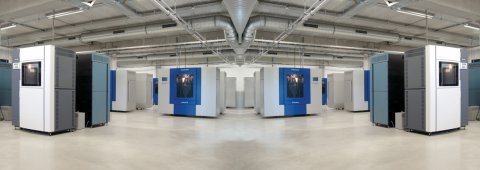
But seriously
Bart van der Schueren from the Flemish company Materialise, which has been active in the field for over fifteen years, showed it can. The company operates more than 80 3D-printers in halls that are the epitome of the clean and white factory of the future. Materialise is particularly strong in biomedical applications, of which in-ear hearing aids are the most widespread. In fact, all current in-ear hearing aids are 3D-printed for a perfect personal fit. Other applications that Van der Schueren showed at the Amsterdam seminar were a cartilage stent for a new born baby and an intricate base for a hip-implant for someone with very little hipbone left. Such objects are designed and printed on the basis of CT-scan and MRI data.
Such success stories notwithstanding, Van der Schueren also told his audience that 3D-printing is a slow, dusty and expensive technology which only makes sense for small personalised objects. “If it is larger than a tennis ball, you need to have a really good reason to choose 3D-printing,” he said.
Wilma Koolen-Hermkens from TNO Additive Manufacturing agreed. 3D-printing first only made sense for hobby and prototyping, she said, and then dental implants became lucrative and as well as other medical devices. But there is work to be done before 3D-printing can enter the high-tech industry. In particular TNO, together with a number of industrial partners and universities, works on improving the reproducibility, enlarging the format beyond the current 60 by 80 centimetres, improving the precision, enlarging the choice in materials and looking for ways to use mixed materials in a single objects. TNO hopes to achieve some of these goals within the next five to ten years.
For industrial designers, 3D-printing offers interesting new opportunities and challenges. At the low-tech end, the technology enables them to produce forms and objects for affordable prices, and perhaps open up a business by selling their work over the web.
At the high-tech end, there is a lot to be learned about the material properties of 3D-printed objects, especially when made from different materials. Materialise, for example, performs old-fashioned tensile strength tests to get data on the materials, which they then use to improve their designs. That’s how they achieved a 3D-printed car seat weighing 7 kilograms instead of 60. Or a 3D-printed fluid switch that is twelve times smaller and 28 times lighter than a conventional one.
Such products may well be the first signposts towards a new, lighter, stronger, smarter and cleaner manufacturing industry.
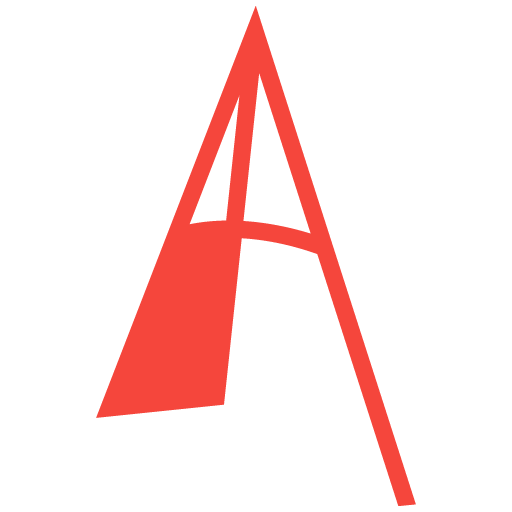
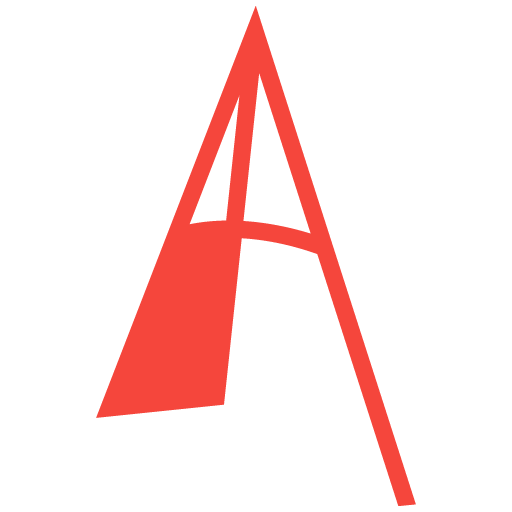
Comments are closed.